Floor Care and the Art of Good Communication
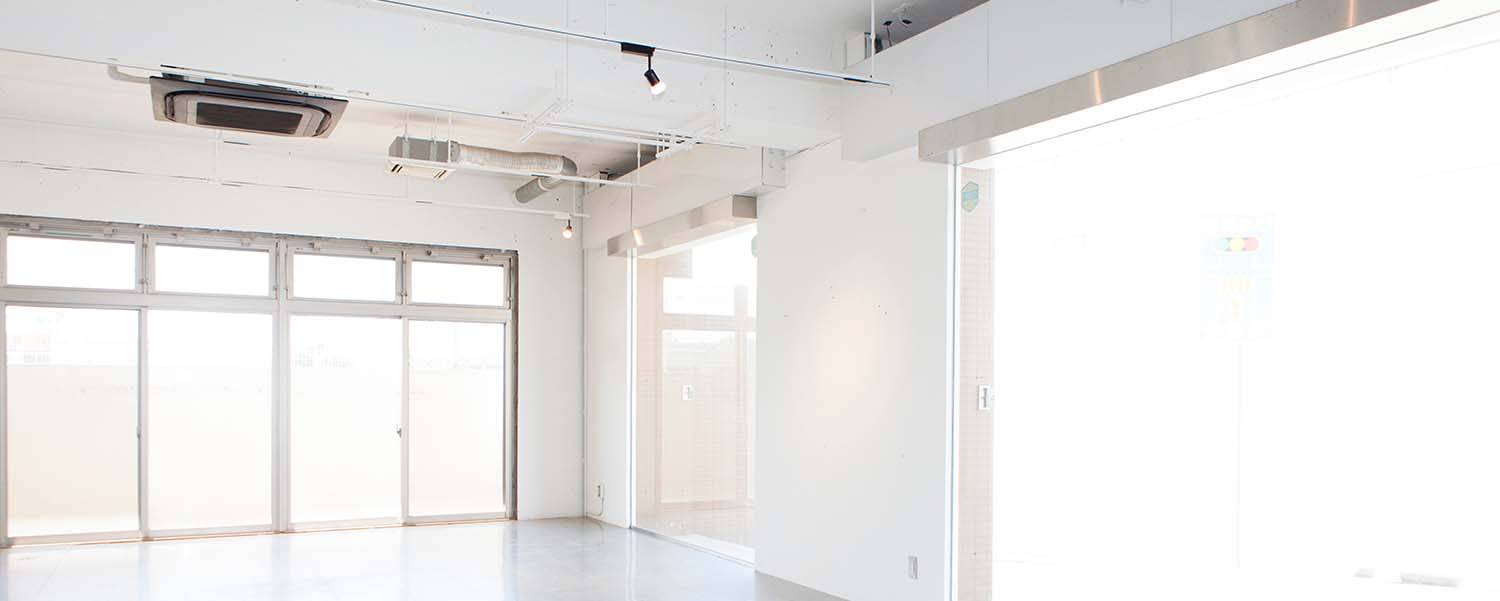
After reading the title of this article, you might wonder, “What does communication have to do with floor care?”
Let me tell you about a particularly enlightening experience of my own. Our emergency department at Wentworth-Douglass Hospital in Dover, New Hampshire, hadn’t been renovated in more than 20 years. It’s far too busy of a department to close down. After having some initial discussions on the topic of renovations, I received an email invitation to a construction-planning meeting for the emergency department.
Our facility had engaged a firm fluent in hospital interior design. Apparently, the planning process had been underway for some time—the emergency department staff had already reviewed concept drawings as well as color swatches and sample pieces of countertop, flooring, wall coverings, and millwork.
Collaboration for this project was key. The planning meetings included the emergency department nursing leadership; the plant operations director, supervisor, and manager; the construction project manager; the environmental services (EVS) director and operations manager; and members of the information systems team.
Once I heard that the emergency department was getting a face-lift, I began lobbying that any new flooring they install be a low-maintenance product. Because our emergency department is so busy, we often have to beg, plead, and cajole the nursing team into letting us close down sections of the department for a time so we can strip the flooring and apply floor finish. Unsurprisingly, arranging the time to perform this maintenance is like pulling teeth, and we seldom get the opportunity.
I asked for the flooring manufacturer’s recommended cleaning instructions and a list of recommended cleaners, along with some sizable flooring samples, so I could be sure that our cleaners and chemicals wouldn’t adversely affect the flooring options.
The flooring that they eventually chose to install was a no-maintenance rubber with a slight texture and a wood-grain look. I wasn’t thrilled with it, but we felt we could make it work. After reviewing all the manufacturer’s recommendations for cleaning and products, I attended another meeting with the emergency department nursing staff, plant operations, the decorators, and factory representatives. The plan was approved, and we scheduled weekly progress meetings.
EVS was focused on how to clean the new flooring. The manufacturer’s instructions were simple:
General precautions
Always use wet floor signs or caution tape when performing wet cleaning.
Refer to safety data sheets for personal protective equipment requirements before using cleaning products.
The floor will be slippery when it’s wet or contaminated with foreign materials; promptly clean up spills and any foreign materials to maintain the flooring’s slip-resistant properties.
Never use grit brushes or black, brown, or any other diamond cleaning pads.
Use a light green, red, or blue cleaning pad for all surfaces unless a different pad is specified in the flooring’s maintenance guide.
To reduce the dirt, debris, and moisture coming into the facility, maintain walk-off mats at all exterior entry points.
Spots from petroleum-based products such as grease and tar must be removed with spotting agents containing solvents; immediately rinse the floor with water after spot removing and allow it to dry.
To increase the shine, dry buff the floor using a white pad.
Do not allow any metal furniture or trash cans to be in contact with the wet floor.
For areas with construction damage, contact the manufacturer’s technical department.
Follow the facility’s standard operating procedures.
For specific written cleaning protocols, contact the manufacturer’s technical department.
Post-installation maintenance
A general cleaning must be performed before the area is occupied. Wet adhesives must be allowed to cure for 72 hours post-installation, and then general cleaning can be performed immediately afterward. If joints or seams are cold-welded, the flooring can be wet-mopped after eight hours, machine-scrubbed after 24 hours and, if required, burnished after 72 hours.
The following procedures should be performed by the EVS team at the facility:
Dust-mop or vacuum the floor to remove dirt or grit.
Remove any adhesive residue and spots of foreign material using a window cleaner or a general solvent.
To remove the production residue, wet-mop the floor using a high-pH cleaner (pH of 12–13) diluted per the manufacturer’s mixing instructions; allow the solution a minimum dwell time of 10 minutes.
Scrub the floor thoroughly with a floor scrubber using a blue cleaning pad; use a pad holder with a red pad for wallbase cleaning and in areas where floor scrubbing machines do not reach.
Wet-vacuum the soiled solution; rinse the floor with clean water and allow it to dry.
To increase the shine, dry-buff the floor using a white pad.
Daily maintenance
Dust-mop or vacuum the floor to remove dust and dirt.
Damp-mop or auto-scrub the floor using a light green, red, or blue cleaning pad with a neutral cleaner diluted per the manufacturer’s mixing instructions, and use a pad holder with a red pad for wall-base cleaning and in areas where floor scrubbing machines do not reach; use microfiber mops for better dirt removal.
The construction phases took weeks. The emergency department was not going to close, but the nursing team would give up several rooms and sections of corridor at a time. Once the flooring was installed, EVS would be allowed to come in and clean according to the manufacturer’s post-installation maintenance guidelines outlined above. The floors had very little shine, and we followed the instructions exactly. After we completed an area, it was released to the nursing team the following morning for patient care.
It didn’t take long for the nursing staff to start complaining about the way the rooms looked. The floors immediately showed scuff and wheel marks, and dirt readily adhered to the floors. We followed the manufacturer’s daily maintenance directions to no avail. The floors still looked horrible. The installers and plant operations accused EVS of not following the manufacturer’s instructions correctly. It seemed that we were battling everyone over the condition of the floors. Plant operations contacted the manufacturer, and they sent us the same instructions, as listed above.
Still the problems continued, and EVS was made to look as though we couldn’t follow simple instructions. Finally, in desperation, we convinced the manufacturer’s representative to visit our facility.
When we spoke to the rep on the phone and explained all that we had done to maintain the floors, he requested that we have a high-speed machine available and a bucket and wringer set up for his visit. He suggested a high-speed burnish that we should order and have available, and he said he would bring pads with him.
It turned out that the rep brought diamond pads made by the flooring manufacturer for the rubber floor—diamond pads that were not mentioned in the care instructions—which he then used to prep the floors. He explained that we needed to use these pads after installation and once the floors began to lose their shine and if scuff marks appeared.
I pointed out that nowhere in the manufacturer’s instructions did it say that we were to use a burnish solution and diamond pads. He told me that the manufacturer purposely withholds that information so that its competitors don’t find out about it. I said, “You know, you could have told us this weeks ago and it would have saved us a lot of grief!” He could only apologize.
So… what does good communication have to do with floor care? Everything!