Green=Green
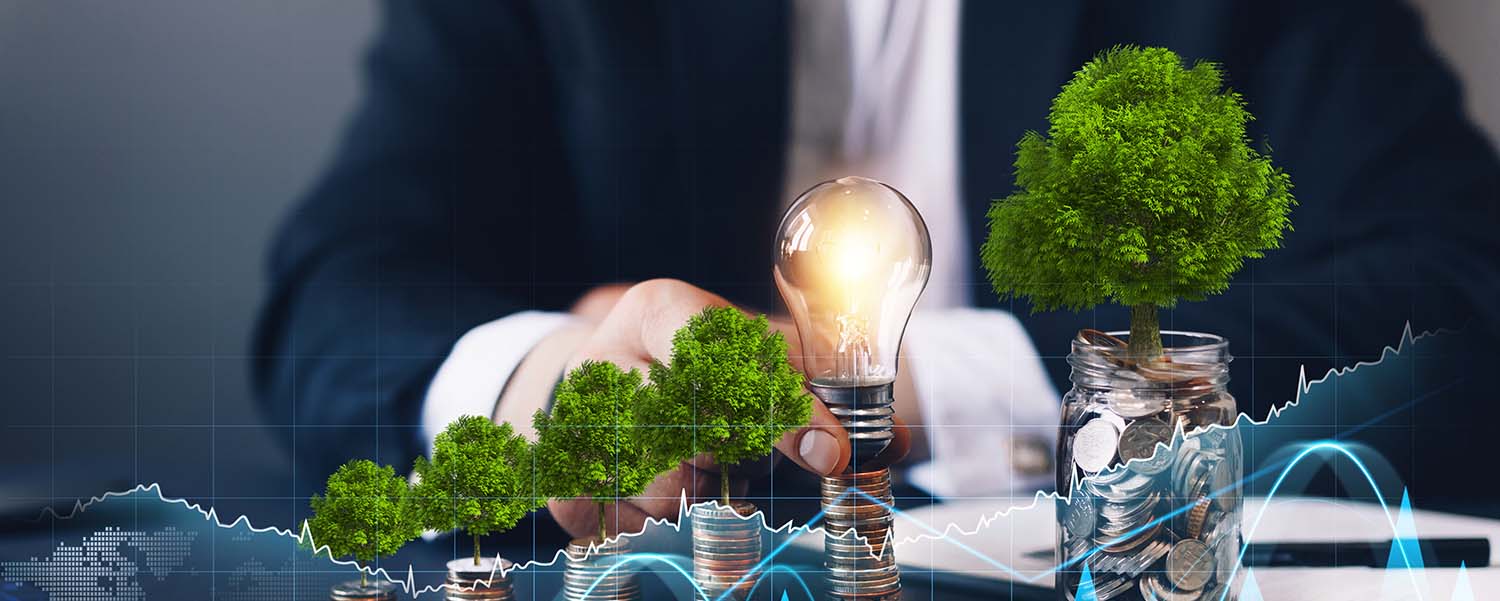
This article will use a case study to illustrate saving opportunities, including a detailed discussion on the financial returns, along with some commonly missed opportunities that can be found on those hard to interpret utility bills. It will also present some best practices moving forward that can be helpful to even small- and medium-sized enterprises.
Increasingly large publicly traded corporations, universities, and other public purchasers are requiring sustainability efforts and reporting from their suppliers as part of doing business. Thus, improving facility performance and operations is not only the right thing to do for the environment, but these actions also generate savings that reduce operating costs, improve the value of your property, and create a safer and more comfortable indoor environment for customers and employees.
Implementing facility improvement measures can reduce annual energy and water utility costs by 10% to 30%, while also reducing associated maintenance and operation costs. These improvement measures are affordable and will complement other green and sustainability initiatives. The return on investment for these projects typically exceeds 25% (less than a four-year payback period) and can often be subsidized in whole or in part by local utility organization incentives that reduce the project costs.
Case study
There can be many variables that contribute to a successful energy and water efficiency project, as illustrated in the following financial summary of an efficiency program for a 50,000 square foot mixed-use facility:
$75,000 annual utility spend ($1.50 per square foot) comprised of:
- $50,000 electricity.
- $15,000 natural gas.
- $10,000 water and wastewater.
In this case study, four efficiency measures were implemented after an analysis of ten potential measures.
The above efficiency measures would apply to many buildings that are greater than 25,000 square feet. These buildings all utilize lighting and HVAC systems; utilize water for domestic, process, and/or irrigation purposes; and have some sort of building envelope (structure). The efficiency measures were selected in this case due to their ease of implementation and attractive return on investment. Other considerations when developing these types of programs include:
- Occupant comfort and safety.
- Operating hours.
- Code compliance.
- Indoor air quality.
- Working conditions.
- Current system reliability issues.
- Positive impact on system uptime.
- Reductions in maintenance and operations expenses.
Financial overview
The financial impact of this project is summarized below:
- $91,000 first cost for implementation.
- $22,125 utility rebate.
- $68,875 implementation cost after utility rebates are applied.
- $18,000 annual utility budget savings and maintenance cost avoidance savings.
- $12,500 annual electricity savings (25% of this utility budget category).
- $850 annual natural gas savings (6% of this utility budget category).
- $1,000 annual water and wastewater savings (10% of this utility budget category).
- $14,350 annual energy and water savings (19% of these utility budget categories).
- $4,450 annual operations and maintenance cost avoidance savings.
- 3.7-year simple payback period.
- 27.3 % Program Return on Investment.
This project is representative of many efficiency programs implemented over the past couple of decades. The positive impact of these projects is often understated since they do not account for increases in utility rates, carbon footprint reduction, property value increases, tax deductions due to IRS Section 179D, depreciation, and eligibility for a change in utility rate classification.
Avoided cost
One additional consideration that is commonly not considered in the investment analysis is the “avoided cost.” This takes into account the rate increases that occur year over year. It monetizes how much an organization avoided spending after adjusting for rate changes. Sometimes this is the only way an organization can understand their true “savings” when looking at their actual spending, because their utility rates may increase faster or equal to the rate they are reducing consumption.
One startling outcome of this analysis is the realization of how fast rates are increasing. Based on data published by the U.S. Energy Information Administration (EIA), commercial electricity consumers in almost 80% of the states nationally experienced an electricity rate (cost per kilowatt-hour) increase from 2020 to 2021, with some states having electricity rates increase by almost 20%1 in just one year.
Calculating the avoided cost can be particularly helpful after an improvement is made to understand how these rate increases impact your savings. Calculating the avoided cost requires a year-over-year rate analysis (i.e., the total cost per unit consumed).
Considering this information, let’s locate an organization in New York, where there was a 16% rate increase for commercial electricity from 2020 to 2021. The organization paid $50,000 in 2020 in electricity. If this organization invests in a lighting retrofit, it has the potential to reduce the electricity cost by 20%, paying $40,000 a year, not taking into account the rate increase. However, due to the rate increase, they end up paying $46,451, but the avoided cost is not captured here.
To understand the avoided cost, analyze how much this organization would have paid in 2021 without doing the lighting retrofit and applying the 16% rate increase; therefore, in 2021, the organization would have paid $58,064 if they did nothing and had the 16% rate increase. The avoided cost equals what the organization would have paid ($58,064) minus the energy savings ($10,000) minus what the organization actually paid ($46,451), equaling the additional $1,612 in avoided cost.
In this example, the organization does see an actual saving to their overall electricity cost because the percent decrease in consumption (20%) was higher than their rate increase (16%). Still, this does not occur in many instances, so understanding the avoided cost is the only way an organization can realize its true financial savings.
Additionally, this rate analysis can identify other potential areas for improvement, particularly in states with deregulated energy markets where consumers can purchase electricity and natural gas supply on an open market. Often supply companies provide very competitive rates while under contact, but if the customer does not actively renew the contract, the rates can increase by 30% or more. Since these contracts can be for many years, it is common for customers to forget to renew.
Understanding utility bills
Businesses typically pay several utility bills every month. There are often opportunities to reduce costs in several utility categories, including electricity, natural gas (or an alternate fuel), and water/wastewater. A utility bill audit of one monthly invoice can identify common mistakes and unnecessary charges. These excess charges include:
- Utility rate class: It is the facility’s responsibility to ensure they are utilizing the optimum utility rate/tariff. This can change as new rates/tariffs are introduced and others are eliminated. Changes in facility use can also adversely impact utility costs and may justify changing the utility rate class.
- Utility inappropriate or excessive sales tax: Some facilities may be exempt or partially exempt from utility sales tax based on their industry type and applicable state sales tax exemption statutes. Industries that may fall in this category include agriculture, mining, manufacturing, residential, and research and development.
- Incorrect account or meter information: Facilities occasionally pay for utility costs for buildings that are not theirs. This occurs most often when utility customers change locations or have numerous properties such as municipalities.
- Late fees: A streamlined utility invoice review and payment process can eliminate or reduce unnecessary late fees. Some organizations outsource this process to eliminate these charges and, at times, secure a discount for the customer.
Best practices moving forward
Larger organizations often have professional staff who are well-versed in energy efficiency practices and can self-implement programs with the assistance of their local utility organization representatives. If capital budget dollars are unavailable, companies can avail themselves of third-party financing and/or utility on-bill finance programs where available. Organizations that do not have this expertise in-house have several options at their disposal if they want to improve their organization’s efficiency, as well as pursue organization goals with respect to sustainability and carbon footprint reductions, such as:
- In-house staff training from organizations such as the Association of Energy Engineers. (www.aaecenter.org)
- Contact their local utility companies for educational assistance and information on potential rebate funding programs. You may also look for information on national websites, such as www.dsireusa.org.
- Utilize the expertise of mechanical and electrical contractors that already perform services on-site if they have experience in energy efficiency programs and have demonstrated success in this field.
- Interview local energy efficiency companies, sometimes referred to as energy service companies (ESCOs), to determine if this is an avenue that may work for your organization. In this scenario, the implementation organization provides financing and implements the complete program.
You can also simply contact a qualified energy efficiency consultant who can guide you through the above alternatives and plot the best course of action for your organization.
A final option, retaining the status quo, may no longer be acceptable today in light of increasing utility costs, the increasing customers’ preference for green products and services, and industry competitors that become more efficient by implementing green and sustainability practices.
Sources:
1 https://www.eia.gov/electricity/monthly/epm_table_grapher.php?t=epmt_5_6_a