Measuring Cleaning Performance
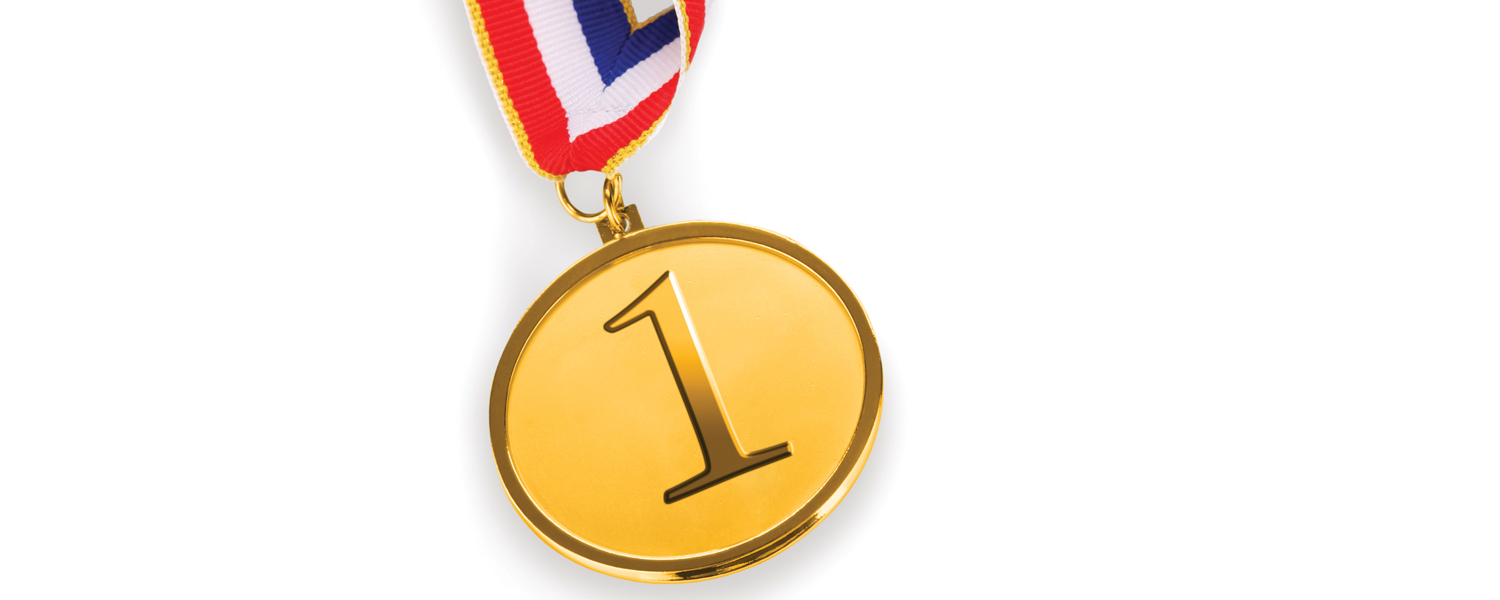
Do it like the Olympian you are.
While Olympic athletes compete in more than 30 sports, following established rules to reach a goal or finish line, cleaning operations perform at least 30 functions adhering to set guidelines and rules, with the goal of removing unwanted matter. See sidebar “30 Functions of Cleaning.”
Just as judges measure and assess the performance of athletes at the Olympics, cleaning managers and customers judge, measure, and assess cleaning performance based on a scope of work (aka, the finish line).
Take aim
There is perhaps no greater “business Olympics” coach than the late W. Edwards Deming, the American who taught the Japanese—most notably Toyota—how to produce great results using a systems approach.
Deming taught that performance is based on the aim of the system. He used the analogy of cleaning a table to illustrate how the system’s aims differ depending on whether the table is used to serve food in a restaurant or to support surgery in a hospital operating suite.
Standardize
Deming also taught the importance of standardizing the system by creating standard operating procedures (SOPs) that are based on a well-defined aim or goal to achieve consistent results.
Cleaning SOPs outline how the cleaning department or operation functions, detailing what is done, by whom, how cleaning tasks are performed, how often, and how results or performance are measured.
Ask questions, apply criteria
Just as Olympic judges ask questions and apply criteria to determine athletic team performance, facility professionals do the same to assess cleaning performance. These questions and criteria include the following:
- Completeness: How well did the team cover all the areas and surfaces they needed to clean? Did they miss any spots or leave any dirt behind?
- Effectiveness: How well did they remove unwanted matter from surfaces? Did they use the appropriate tools, techniques, and chemicals for the type of dirt and surface?
- Speed: How quickly did the team complete the cleaning task? Did they meet or beat the expected time? Did they balance speed with quality?
- Safety: How well did workers follow the safety rules and regulations for the cleaning task? Did they wear the proper personal protective equipment (PPE) and handle the chemicals safely? Did they avoid injuries or accidents?
- Sustainability: How effectively did the team minimize the environmental impact of the cleaning task? Did they use greener products and practices? Did they reduce waste and conserve resources?
- Budget: Does the process reduce or add costs to the system? What are the short-term versus long-term financial impacts?
- Ambient environments: Does the process affect indoor air quality? How quiet or noisy is it? Does it introduce chemicals, particles, respiratory irritants/sensitizers, or petrochemical-derived fragrances to the indoor space? Does it have undesirable side effects related to ergonomic strain, particle exposure, or chemical exposure?
- Customer satisfaction: Are customers happy with the cleaning as defined by the scope of work? Would customers be happier if the scope were expanded?
Looking closely at performance
When scoring figure skating, Olympic judges closely examine elements such as the difficulty and execution of a triple axel, double lutz, triple salchow, double axel, spin combination, step sequences, as well as the level of artistry and innovation.
When judging cleaning performance, the tools used for measuring and determining scores include:
Visual inspection: This is the simplest and most subjective method of assessing cleaning effectiveness. It involves looking at the surface or object before and after cleaning and judging whether it appears clean or not. Visual inspection can be useful for detecting obvious changes, such as the removal of visible dirt, dust, or stains. Still, it cannot detect microscopic or invisible substances like bacteria, viruses, and mold spores. Using an invisible-ink fluorescent marker on surfaces prior to cleaning, followed by a black light inspection afterward, can reveal what areas have been cleaned and non-cleaned areas for retraining and validation purposes.
DNA reactant: This method involves spraying the surface with a chemical marker that reacts with the DNA of specific microbial contaminants, imaging the results with a UV light camera, and then uploading the images as visual proof of where germs remain after cleaning. A DNA-reactant system can be very useful but may require specialized and costly equipment and expertise, though leasing options are available to reduce costs.
Colorimetric test: This method of measuring cleaning effectiveness uses a color indicator that changes color when it reacts with a specific substance. For example, you can use a colorimetric test to detect the presence of blood, protein, or detergent residues on a surface or object. Colorimetric tests can be more objective and sensitive than visual inspection. Still, they can also be affected by other factors, such as the background color of the surface or object, the lighting conditions, and the interpretation of the color change.
Microbiological test: This method measures hygienic effectiveness using a microbiological indicator or growth medium to show the presence or absence of microorganisms, such as bacteria, fungi, or viruses, on a surface or object. Examples include Petri dishes, RODAC plate sampling (RODAC stands for Replicate Organism Detection and Counting), and fungal enzyme detection. While microbiological tests can be highly accurate and reliable, they can also be costly, time-consuming, and require specialized equipment and expertise.
Chemical test: This method measures cleaning effectiveness using a chemical indicator that shows the concentration or activity of a chemical substance on a surface or object. For example, you can use a chemical test to measure the pH, hardness, or chlorine level of water or the amount of detergent residue on an object. ATP meters detect the presence of organic soils on surfaces by detecting ATP found in food residues, body fluids, and other organic matter. While chemical tests can be helpful, other chemicals, temperature, or pH can also influence them.
Budget analysis: Variance analysis compares the actual results of a budget period—such as revenues, expenses, profits—with other regimens and budgets, examining the differences and identifying possible areas for improvement.
Particle counters: These devices can measure airborne particles ranging in size from .1 to 10 microns. A handheld particle counter can reveal whether a sealed-body vacuum cleaner is releasing dust by measuring the air being drawn into the vacuum and then comparing it to the exhaust air.
Table-top particle counters are useful for long-term monitoring of indoor areas to detect patterns, peaks, or spikes. For example, a period of elevated airborne dust during “cleaning” times may indicate the use of inefficient methods of dusting (e.g., feather dusters) that tend to stir dust.
Some wall-mounted room air quality sensors can detect particles as small as .1 microns, VOCs, and even the presence of airborne pathogens (be sure to request test data—trust and verify).
Productivity:
- Time studies that record the time spent by a worker on each task and calculate the average time per task help management compare actual times with the expected times, identifying any discrepancies or inefficiencies. ISSA’s Cleaning Times guidance is helpful here.
- Work sampling involves observing a cleaning worker at random intervals and recording the type and quality of the work performed. This helps assess the frequency and distribution of the tasks, as well as the consistency and accuracy of the cleaning.
- Performance ratings involve assessing a worker’s performance on a scale based on predefined criteria, such as cleanliness, completeness, and timeliness of the work. This provides feedback and recognition, helping set goals and incentives.
- Customer feedback involves gathering input from building occupants, visitors, or clients to help assess customer satisfaction, productivity, and the impact of cleaning on the image and reputation of the building.
Human environment scoring: Workers’ compensation and insurance claims, observations, surveys, and human resource data can help assess working conditions and customer satisfaction. Keep detailed records, use checklists to ensure PPE compliance, and work with risk management to track trends. Interviews and surveys are also helpful tools for measuring and improving overall customer satisfaction.
Sampling
Just as Olympic performance is evaluated by averaging the scores of many judges, it is important to gather multiple surface samples to obtain meaningful and representative results of the cleaning. For example, if using an ATP meter to measure the reduction of organic soils, sample half a dozen surface locations and then average the results.
Applying the information presented here will help cleaning operations bring home the metaphorical bronze, silver, or gold in their quest for measured excellence, highlighting the vital role of cleaning workers in the Olympian task of cleaning.
Allen P. Rathey, director of the Indoor Health CouncilTM (IHC), is an educator specializing in healthy facilities. He has assembled an advisory group of scientists, PhDs, and facility and public health experts who share his passion for helping people everywhere create and maintain safe and healthy indoor environments.
General Testing Concepts
Measure. Use one or more measurement tools to determine which areas in the facility most need cleaning and assess how effective current cleaning methods are. This helps establish a baseline of current practices.
Compare. Establish benchmark data in an Excel or similar spreadsheet, creating a database that facilitates the comparison and improvement of cleaning practices.
Experiment. Facility managers should explore new and varied cleaning and disinfection methods to determine what works best.
Implement. Once effective methods are identified, they are integrated into regular practice, with ongoing measurements to ensure continuous improvement.